Chiclets line,Xylitol Tablets machine
This machine includes the chiclets line,chiclets wrapping machine.
This kind of pelletes of”chiclets-shape”,or chiclets line,chiclets machine including following machines:
1. Automatic Coating Pan TW-CT-400 CLT
2. Double Jacket Serve Tank with Stirrer and Electric Heating
3. Double Jacket Wheeled Syrup Tank
4. GF Automatic Air Humidity Control System for Coating Pans
5. GF Cooking Unit for Sugar Syrup with Pump
6. GF Polishing tanks
7. GF Pillow pack machine GF-PL-1000/SP.2IN1
Attachment: Technical description
Item 1.Technical Description
GF Mixer TW-MX-300/UN
GF mixer type MX-300UN is a new design of machine based on the advances German technology. They are widely used in the fields of Bubble Gum, Chewing Candy, Chemical and Pharmaceutical industries.
The main structures:
The trough and the mixing blades are made of stainless steel which are easy to clean and offers a long service life.
The mixing blades of the mixer are of “z” shape, which can be used not only for mixing and kneading, but also for stirring, blending, beating, homogenizing and plastifying of the ingredients. The clearance between the wall and blades is very small to avoid the retain of the gum mass.
Take the advantage of the opposite rotation and inch-stop performance of the mixing blades, as well as the tilting function of the trough by means of the worm gear and screw driving system, makes the discharge of the ingredients very easy, safe, reliable and sanitary.
Double-jacket of the trough is provided for heating up the gum mass, and can be connected to its own heating system for warm water circulation.
The electric components and control system are of reliable and safe design with interconnection of various functions according the International standard.
Technical Data:
The capacity: 300 Liters
Tilting angle: QMAX=90о
Main motor: 22 kw
Motor for tilting system: 2.2kw
Motor for water pump:t 0.5kw
Water heating: 2×2 kw
Total power consumption: 23.75 kw
Blade Rotation speed: 19 rpm-28.5 rpm
Heating water temperature: ≤100℃ adjustable
Power supply: to be confirmed by the client
Machine weight: 3500 kg
Overall dimension: 2700X1600X1700mm
chiclets line,chiclets machine CO-EXTRUDER TYPE TW-EX-100×2/CG
Co-extruder type GF-EX-100×2/CG is capable to offer 2 ropes of chewing gum with capacity of up to 600kg/hour. This machine is equipped with advanced electrical control system and mechanical conveying structure.
MECHANICAL CONSTRUCTION
The extruder is equipped with two barrels mounted on one frame, each barrel with two F 110 infeed rollers and two F 100 extrusion screws attached.
Two sets of 60-liter hoppers on top of the barrels are built in two parts. Various forming dies are properly designed as requested, correspond to different shapes of product.
The extruder is equipped with three individual heating units. Heating or cooling of the barrels is controlled respectively by three water tanks via three thermo-regulators with digital display. Automatic adjustment starts when temperature has been set. The set temperature and the actual temperature are shown on the display.
The gearboxes are also installed on the extruder. Each unit includes gears gone through thermal procession. All axles are fixed on a ball bearing. The gears and the bearings run in an oil bath. The hydraulic reservoir is filled with special oil resistant to high-pressure. An electronic over-pressure protection device is fitted in each barrel accurately controlled by a microprocessor.
ELECTRIC APPLIANCES
Two A.C. frequency converters together with main driving motors are introduced to infinitely adjust the extrusion speed.
Each set of extrusion screws is assigned with a variator to regulate the ratio depending on various raw materials to be extruded. “Speed Up or Down” Operation is achieved by a variator when the ratio has been fixed.
The extruder is equipped with three thermo-regulators with temperature display. All electric components and adjustment device are positioned at eye’s level. All contactors, relays and fuses are installed in the control cabinet.
TECHNICAL DATA:
Extrusion capacity:
|
Up to 600 kg/hour
|
Number of candy ropes:
|
2 rope(s)
|
Extrusion screw dia:
|
100 mm
|
Infeed roller dia:
|
110mm
|
Motor power:
|
2X5.5 kw
|
Power for water-heating:
|
3X6kw
|
Motor protection:
|
IP 55
|
Speed adjustment range:
|
1:27
|
Water consumption:
|
300lt/hour
|
Machine weight:
|
2300 kg
|
Overall dimension:
|
2350×1570×1550mm
|
chiclets line,chiclets machine Rolling Machine type GF-RL340CG
The machine takes over the chewing-gum sheet coming from the extruder and powders it at both sides. The thickness of the chewing-gum sheet is reduced and rolled out to the final thickness and the surplus powder material is brushed off. Then the gum’s sheet is cut into the desired dimensions. The pre-cut gum slabs are fed onto wooden trays and piled. Different kinds and dimension of chewing gum or Chiclets can be made by changing cutting knives.
Mechanical Construction
1. Infeed conveyor belts
Two endless infeed conveyor belts coated with silicone material are fitted. The top infeed conveyor belt can be tilted down to have sufficient space when opening the die plates. There’s a powdering device on both top infeed conveyor and bottom infeed conveyor. The device can automatically drop powder onto the upper and lower surface of the gum slice, which is to be transmitted to the first set of rolling stations.
2. Rolling Stations
There’re 3~4 sets of stainless-steel rolling stations to reduce gradually the thickness and density of the chewing-gum sheet. The upper and lower roller sets apply cooling-inside structure, which can help to reduce the usage of lubrication.
The gap and parallel of all roller sets is adjustable by means of hand wheels. Each rolling station is equipped with scrapers for cleaning as well as protective bars.
3. Cutting rollers for lengthways cut
The knives’ distance and the parallelism can be changed by adjusting the cushion to meet requirement on the width of gum sheets. The scraps on both sides will be automatically removed by the cutting knives during movement.
4. Cutting rollers for cross cut
The knives’ distance and the parallelism can be easily adjusted. The length of gum sheets can be modified by adjusting the running speed.
5.Separating belt
Behind the cross cutting station a conveyor belt for the circulated separation of the chewing-gum sheets is mounted. The cut gum sheets arriving on the separating belt will be automatically separated and transmitted to wooden trays.
6.Powdering device
On top of the top and bottom infeed conveyor belt one powdering device each is mounted. The powdering quantity can be adjusted but the powder should have been treated by drying. ⑺ Lighting
A capped lighting is installed over the rolling and cutting stations to guarantee optimum sight conditions at the line.
7. Brushing-off device
Between the second and the third rolling station an endless conveyor belt is installed. One brushing roller each is mounted on top and behind the conveyor belt. The brushing rollers can be adjusted to brush off redundant powder. And the powder collecting system is fixed in order to keep the working areas with clean air.
8. Scraps collecting conveyor
At the rear side of the machine a scrap return conveyor belt is provided. The lateral scrap are fed by a conveyor belt to the machine end onto a cross conveyor belt and then onto the scrap return conveyor belt. The scrap strips are then fed back to the extruder by means of various conveyor belts.
9.Product change
The cutting roller sets are slipped on the drive shafts. For exchanging the cutting rollers, the shaft bodies are removed and replaced through other ones with the desired product dimensions. The product change can be effected within a few minutes.
10 Dust Collecting Device
The powdery particle which is blow up by the powder brushing device can be absorbed by the dust collecting device and deposited in the depositing device. The filtrated air will be sent back to the workshop. The dust collecting device is composed by fans, filters and depositing device.
Electrical equipment
The electrical control and regulating instruments are clearly arranged.
All contactors, relays and fuses are installed in the control cabinet.
Technical Data
Max Capacity: up to 400 kg/hour
Total Power: 10 kw
Motor: to be confirmed by the client
Protective System: IP55
Speed adjust range: 1: 6
Outer dimension: 6800×1500×1700mm
Automatic Packaging Machine for Stick wrap chiclets line,chiclets machine
Chewing gum automatic packaging machine type SK-1000-I is one of the patent products of Sanko company (Patent Series: 200420073162X). It consists of two parts: automatic cutting machine and automatic packaging machine. The automatic cutting machine cuts the cooled chewing gum slice into required packaging pieces and conveys into the packaging machine. Then the packaging machine can complete the wrapping automatically, including silver paper wrapping, outer paper wrapping and stick wrapping for 5 pieces. The machine is featured as stable and reliable during the whole procession.
The machine adopts advanced electronic components and PLC control system, the wrapping speed is adjustable by frequency converter. By use of photocell tracking system and auto-compensation, the machine can follow the eye-mark precisely and reliably. Detecting, censoring components and photocell tracking system are fixed onto relevant position of the electrical control system. By use of touch screen as human-machine interface system, the operator can easily set, change or save parameters during wrapping. All the transmission parts are fixed with safety and noise deadening cover. A photoelectric safety system was fixed on the operation side of machine which can protect the operator well. This machine is specialized in high-speed wrapping of chewing gum.
Main Technical Parameters:
Capacity: 650pcs/min depending on exact dimensions and hardness to be confirmed
Total power consumption:6KW
Total weight: 2600kg
Control system: PLC, touch screen, adjustable speed controlled by frequency converter, photocell detecting system, mechatronics controlling.
Overall dimension: 5000mmx2000mmx2000mm, LxWxH
Working condition: Temperature 18-21℃; humidity 45-55%
Specification and requirement of packaging material:
Alu. film reel:
Max. outer dia.: Ø 340mm; Width:92mm; Inner dia.: Ø76±0.5mm
Inner paper reel:
Max. outer dia.: Ø 400mm; Width:68mm; Inner dia.: Ø152.5mm
Length between two photo mark centers: 52±0.2mm
Outer paper reel:
Max. outer dia.: Ø 350mm; Width:94mm; Inner dia.: Ø76±0.5mm
Length between two photo mark centers: 78±0.2mm
Item 2.Technical Description
Automatic Coating Pan GF-CT 400-CLT for chiclets line,chiclets machine
This machine is designed for the automatic coating for tablets, pills and similar products. By adopting advanced technique. It is easy and reliable in operation.
Operating Principles
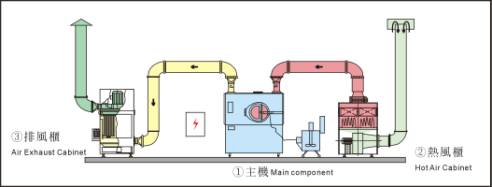
Inside the rotary drum of the coating machine, the bare tablets are made to move along a consecutive and complicated track. In the processing of the motion, controlled by the programming control system, a medium is automatically sprayed( or trickled )to a tablet surface according to the selected technological sequence and parameters by a peristaltic pump and spraying gum (or a drip pipe for sugar coating).At the same time, finely-filtrated clean hot air from hot air cabinet penetrates the tablet bed and then is exhausted from the bottom of the drum and discharged after being dedusted so that a solid and smooth film or sugar coating can be quickly formed on the tablet.
Mechanical Construction
(1) Host machine
It consists of closed operating chamber, perforated coating drum, agitator, washing disk, driving device, air inlet and outlet valve mechanism.
(2)The sugar coating system
The sugar coating system is composed of syrup pump, silicon rubber pipe thermostat agitating vessel, sugar coating trickle pipe.
The coating system is a pneumatic spraying system, which consists of peristaltic pump, silicon rubber pipe and spraying gun.
(3)Hot air cabinet
Hot air cabinet is made of cabinet body, centrifugal fan, filtration system, heat exchanger. The cabinet can directly take in outdoor air, which can meet 100,000 level cleanness requirement through primary, medium, high level filtration with 95% dust powder with dia. More than 5 um purified. The purified air, heated to 80℃ by the heat exchanger, enters the coating drum. The exchanger can be heated by steam or a electric heat rod.
(4)The exhaust cabinet
The exhaust cabinet consists of cabinet body, explosion-proof centrifugal fan, dust-removing system. The cabinet is used to keep the coating drum operating chamber under negative pressure.
(5)The PLC control system
By adopting the PLC control technology, the machine control system is reasonable in design and flexible in programming. Auto/manual mode is available for different coating technology. The system is featured by high anti-interference capacity, little failures, easy maintenance and good expandability.
Electrical appliances:
the main elements and devices in the system, such as contactors and relays and PLC are all of card-board type for easy maintenance.
Technical data
Max. coating capacity: 400 kg/batch
Coating pan dia: Φ1580mm
Feed inlet dia: F475mm
Rotary speed range: 0-13r/m
Main motor power:t 3kw
Exhaust cabinet motor power: 7.5kw
Exhaust capacity: 10000m3/h
Hot air cabinet motor power: 1.5kw
Hot air consumption: 2356m3/h
Cleanness efficiency: 100,000 level
Peristaltic pump or lobe pump motor power: 0.37kw (0.55kw)
Silicon rubber hose: F 9~16mm
Main machine dimension(L×W×H): 2500×1700×2800mm
Main machine weight: 1000kg
Hot air cabinet dimension: 1000×900×2120mm
Exhaust cabinet dimension: 1290×1050×2000mm
Hot air cabinet weight: 550㎏
GF Automatic Air Temperature and Humidity Control System for Coating Pans
1. Technical requirements
Processing air parameter:temperature T≤20℃, humidity RH ≤20%
Fresh air parameter: temperature 40℃, humidity 80%RH
Processing air flow: 10,000m3/h; Fresh air flow:10,000m3/h; Exhausted air flow: 10,000m3/h;
2. The processing procedure of the dehumidifying system
1) Air processing diagram

Wind rate 5000m3/h
Exhausted air10000m3/h
2) Parameters in different stages:
Stage |
A
|
B
|
C
|
D
|
E
|
Air flow m3/h
|
10000
|
10000
|
10000
|
10000
|
10000
|
Temperature ℃
|
40
|
12.9
|
36.9
|
19
|
20
|
Relative humility %
|
80
|
95
|
7.4
|
21.2
|
20
|
Humidity Ratio g/kg
|
39
|
8.9
|
2.9
|
2.9
|
2.9
|
Enthalpy volume kj/kg
|
140.8
|
35.5
|
44.8
|
26.5
|
27.6
|
3) Performance measurement:
front cooler capacity Q1=301770kcal/h=350kw
rear cooler capacity Q2=52180kcal/h=60kw
total cooling capacity: Q3 =352600kcal/h=410kw
3. Main technical data: Dehumidifying machine:
Items
|
Main technical parameters
|
||
Dehumidifying machine ZLB-D-20000
|
Processing air flow (m3/h)
|
10000
|
|
Fresh air flow (m3/h)
|
10000
|
||
Rotor-dealt flow (m3/h)
|
10000
|
||
Cooling water capacity(kw)
|
Front cooler capacity
|
350
|
|
Rear cooler capacity
|
60
|
||
Outlet air pressure (pa)
|
≥300
|
||
Reacting temperature(℃)
|
130
|
||
Reacting power (kw)
|
200
|
||
Processing fan power (kw)
|
7.5
|
||
Reacting fan power (kw)
|
3.0
|
||
Rotor drive power (kw)
|
0.18
|
||
Cooling compressors power (kw)
|
100
|
||
Total power consumption (kw)
|
125.8
|
||
Power supply
|
220V, 3 phases, 60Hz
|
||
Overall dimensions (mm)
|
See machine photo
|
||
Total Net Weight (kg)
|
3500
|
4. Automatic Control and Auxiliary Devices for chiclets line,chiclets machine
Control system of ZLB series use SIEMENS S7-200 PLC as its core. This system gather digital and analog signals from machine’s condition, by means of self-developed program and multiplexing PID control module, it forms a perfect automatic interconnection control system. After the control device analyzed input data, the control device can control the machine’s function. Through internal-set PID’s function, it can adjust cooling duty, reactive heating parts by linear control, so that it can ensure the stability of the temperature and humidity of the processing air. In accordance with the user’s demand, we can set remote control or control by touch screen.
Interface between machine and operator can choose text display or touch screen. All parameters, function condition, troubles can be searched on it; Also control parameters can be set according to various production procedure.
Reacting system sets up multiple protection (Over-heating protection of reactive temperature, reactive heating box, reactive air), reactive fan over loading, rotor motor over loading, rotor stalling and reactive heating chain protection to ensure the security of reactive system and rotors.
This machine is reliable and well designed, which makes it quite easy to operate.
The machine can display and print data/alarm/troubles of previous operation by images. Furthermore, it can set program according to concrete room condition. Dehumidifying device automatically adjust all relevant parameters in accordance with preset temperature and humidity.
5. Main Configuration
Devices & Components
|
Manufacturer
|
Processing Fan
|
Samsung
|
Reacting Fan
|
Samsung
|
Dehumidifying Rotor
|
ProFlute, Sweden
( Rotor with medium of Silica gel )
|
Cooler
|
Processed by OAK,USA
|
Reducer
|
SEW
|
Cooling Compressor
|
COPELAND
|
Relay & Contact
|
Siemens
|
Air Switch
|
Siemens
|
Airproof material
|
Du Pont
|
Temperature & Humidity Probe
|
E+E Co. Austria
|
PLC Controller
|
Siemens
|
TW Cooking System for Syrup
Following machinery included:
set of double jacket tank ( all in stainless steel)
– Capacity: 300Liters
– Steam pressure:4 kg /cm2
– Rotation of the agitator: 40 rpm
– Power Consumption: 0.75 Kw
– Pipeline filter
– One set of rotary Discharge pump
– Rotary speed: 0-400 rpm
– Capacity: up to 0-1200 liters/ H
– Power Consumption: 0.75 Kw
– Reducer and motor: SEW
Remarks: All the material for the above is SUS304
GF Polishing Tank
Brief introduction:
This polishing tank is used to polish dragee surface. It is with motors and diameter of 1,000mm. Both cold air and hot air is required by means of popes in the procedure according to concrete situation.
GF PILLOW PACK WRAPPING MACHINE
(GF- PP-1000/SP.2 IN 1)
This machine suits for the packing of two ready made chiclets in one pack. With special disc feeder, the machine can guarantee for the capacity of 300 packs per minute for the requested packing. By adopting advanced technique. It is easy and reliable in operation.
Main Structure:
1. Safety:
Automatic shows error, safety shield, safety switch.
2. Intelligence:
This system can store products’ parameters more than 100pcs. The touch screen shows everything in English, operation indication, error signal and speed which help it easy for the operation.
High efficiency:
Fast speed, less empty bags ( less than 1%), steady packing capacity. Empty bags automatic removing device. Double film shaft device to reduce time of stop machine.
longevity:
Easy to change the spare parts, whole structure designed for long time usage.
Low noise:
Main Technical Data:
– Capacity: 300 packs per minute for twin chiclets in one pack ( actually the wrapper is designed with the capacity up to 1000 pieces per minute for normal ready made single candy)
– Packing specification: L:12-40mm; W:12-30mm; H:5-18mm
– Length of finished bags: 50-80(Only one size, no need to adjust the length)
– Candy Shape: Square, Ellipse, Oblate, Globular, Plum Blossom-shaped
– Gross Power: 4kw
– Overall Dimensions: 3300x1350x1560
– Gross Weight: 1400kg
– Power: 220v 50Hz
– Packing Material: Hot-sealing materials such as OPP, CPP, PET Metallized film, Al-plastic film, Paper-rubble complex